東麗開發出了重量比以往的GFRP(玻璃纖維增強樹脂)輕約60%、具有同等的彎曲彈性模量的CFRP(碳纖維增強樹脂)。通過采用發泡樹脂那樣的多孔構造,同時實現了輕量化和高剛性。可以使用普通的GFRP用沖壓成型機,制造汽車的地板等部件(圖1)。

圖1 多孔CFRP的試制品
可使用普通的GFRP用沖壓成型機,在5分鐘左右內完成大型部件的一體成型。
東麗將此次開發的材料稱作“CFRF”(Carbon Fiber Reinforced Form,碳纖維強化發泡樹脂)。典型的發泡樹脂——發泡聚丙烯(PP)的比重僅為0.3~0.4,不過彎曲彈性模量只有0.1GPa左右,剛性較低。因此,在汽車領域,發泡樹脂一般被用于對強度和剛性要求不高的內飾材料及隔音材料。
而且,汽車部件使用的GFRP(基體樹脂采用PP的情況下)的比重為1.2左右,按體積比例混入20%的玻璃纖維之后,彎曲彈性模量約為6GPa。而東麗開發的材料不僅比重與發泡PP同等(0.3~0.4),而且實現了與PP基GFRP同等的彎曲彈性模量(6GPa)。
碳纖維立體交纏
據東麗介紹,以往的GFRP需要在玻璃纖維之間不留空隙地填滿基體樹脂,而東麗開發的材料則是讓碳纖維呈立體狀交錯纏繞,形成多孔構造。利用這種構造,同時實現了低比重和高剛性。
從制造方法來看,東麗將連續的碳纖維(直徑約為7μm)切成了10mm左右的長度。將這種碳纖維和基于熱塑性樹脂的粘合劑樹脂混合在一起,在裝有溶液的模具內一邊加熱,一邊使碳纖維均勻分散。然后,在將溶液從模具中排出去的同時進行壓縮,最后制造出多孔構造的片狀或者卷狀基材。按體積比例計算,碳纖維的含量約為20%,空間約占50%。片狀基材可以生產厚度為0.5~3.0mm的產品,卷狀基材可以生產厚度為0.1~0.5mm的產品。
分散的碳纖維的接觸點(交叉點)通過粘合劑樹脂牢固地粘合在一起,形成了碳纖維呈立體狀交錯纏繞的多孔構造。即便在制造基材時進行壓縮,也能保持內部空間(圖2)。粘合劑樹脂的基料——熱塑性樹脂除了PP之外,還可以使用“PA(聚酰胺)6”、“PPS(聚苯硫醚)”等。
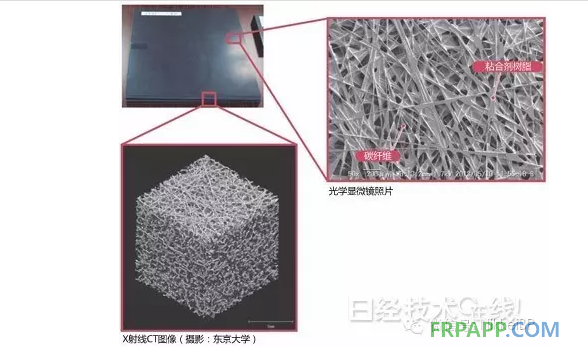
圖2 多孔CFRP的構造
碳纖維的交叉點通過粘合劑樹脂牢固地結合在一起,形成了呈立體狀交錯纏繞的三維構造。
沖壓成型時會沿厚度方向膨脹
把采用這種工藝制造的基材放在模型中,可以使用普通的GRFP用沖壓成型機,加工成汽車部件等。沖壓成型時的加熱溫度方面,PP為200℃,PA6為250℃,PPS為300℃,模具溫度均設定在100℃左右。
據東麗介紹,經過沖壓成型時的加熱,粘合劑樹脂會變軟,同時,制造基材時被壓縮的碳纖維也會在回彈力的作用下沿著基材的厚度方向發生膨脹。這樣一來,各位置厚度不同、形狀復雜的部件也能實現一體成型(圖3)。沖壓成型后一冷卻,粘合劑樹脂與碳纖維就會再次牢固地結合在一起,從而可獲得與以往的GFRP同等的彎曲彈性模量。
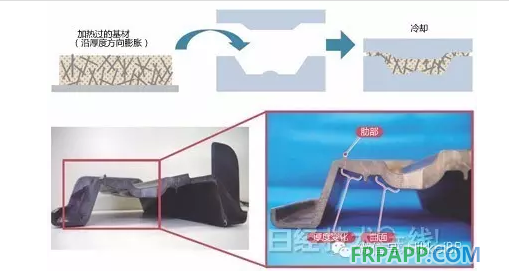
圖3 利用模具的空隙(空間)
經過沖壓成型時的加熱,碳纖維會沿著厚度方向發生膨脹。這樣一來,便可以制造出各位置厚度不同、形狀復雜的部件。
新材料還能用來制造復合構造的成型品。比如內部由此次的材料構成、表面由熱固性CFRP構成的成型品。
目標是3年以內實現實用化
關于此次開發的材料,東麗已開始向汽車廠商及部件廠商提供樣品,計劃3年以內實現實用化。除了發動機罩、車門、后備箱蓋、車頂、地板等板狀部件之外,該公司還打算將該材料應用于要求具有耐沖擊性的保險杠及吸能盒等部件。
不過,新材料的實用化還面臨幾個問題。成型時可以使用普通的GRFP用沖壓成型機,這對于汽車廠商及部件廠商來說是一大優點,但成型需要花費約5分鐘的時間。沖壓成型的時間為1~2分鐘左右,成型后的冷卻時間為3~4分鐘。而GFRP的成型時間為1~2分鐘。新材料面臨的第一個問題是如何縮短成型后的冷卻時間。
另一個問題是成本。目前,東麗使用該公司內部的實驗設備(年產規模為數噸)來生產樣品,成本高于GFRP或CFRTP。對于這一點,東麗表示,“量產時,可通過加入一些設計來發揮能夠立體成型的優勢,將成本降至可與目前的GFRP或CFRP進行價格競爭的水平”。