2017年終碳纖維會議(CarbonFiber2017)如期召開,各相關公司踴躍參加并進行了年終總結。東麗、ELG、波音等企業大咖齊聚一堂,共話碳纖維行業2017的成長與挑戰,并預測2018市場增長情況。
碳纖維行業在過去的一年中取得了哪些成績?2018年碳纖維市場又將迎來哪些重大突破?從會議伊始到結束,一直在為提高應用技術,拓寬碳纖維應用努力著。會議的最后一天節奏稍微放緩,會上做了對碳纖維今年市場增長情況的預測,并通報了幾項最新的技術成果。
碳纖維行業的成長與挑戰
通用汽車公司的工程組經理Mark Voss在會上做了關于碳纖維發展新型汽車應用的演講,系統地闡述了這個方向將會面臨的挑戰。Voss主要研究開發體結構先進復合材料,根據在Corvette車系中應用碳纖維面板的經驗,他建議大家盡可能選擇熟悉的材料形式和加工技術,可控性是新型碳纖維部件的成功關鍵。要盡可能在新應用中限制“新聞”的產生,就是說要限制汽車行業的新技術和流程的數量。因為在碳復合材料中材料和工藝變量本來就很多,當盲目加入熟悉度不高的新事物時,實施結果的復雜性將會被大大增加。他用一個數據作為例證,如我們在A類表面上工作時,變量會被放大100倍。
Voss還強調了連接技術對于引入碳元件的重要性,這些碳元件必須與汽車結構中的不同材料結合在一起。在演講中,他說目前碳材料的成本較高讓碳復合材料的成本競爭力看似很低,但建議大家高瞻遠矚,對比廢鋼的成本,碳纖維才是一條明智選擇。最后他展望了對此次會議成果的期待:“我非常高興看到這個房間在未來20年帶給我們的是什么。”
隨后,來自美國波士頓勒克斯研究所的Anthony Vicari以碳纖維復合材料在未來的成長機會和面臨的挑戰為主題發表演講。首先他對碳纖維行業發展預測數據進行報告,到2020年碳纖維產能能達到151,000公噸(MT)/年,實際產量預計減少約10-20%。到2025年,碳纖維的需求預計將達到22.8萬噸/年,其中風能和航空業增長最快。如果這些數據真的實現了,在2025年之前,汽車上碳纖維的利用普及率將會提高,不再為豪華車型獨享。
他說,在鐵路,建筑維修和大型海洋船舶方面對玻璃鋼(碳纖維增強樹脂材料)的需求將繼續增長。因為在鐵路上應用時,玻璃鋼制轉向架取代鋼鐵的話,可以將鐵路車輛的重量減輕近1公噸,且耐腐蝕性很好,可以提高維護和使用壽命。他還看到了碳纖維在橋梁維修上的大市場,他說目前玻璃鋼的制備和使用技術非常成熟,但基礎設施市場還沒有把目光放到這上面。這一切的激發點只需要等時機成熟,比如等美國LeMond復材所和橡樹嶺國家實驗室開發出低成本的碳纖維,再委托制造商代工生產,由FARO Technologies和Oxford Performance Materials等創新廠商開發的改進修復技術即可完成。
在風能領域,碳纖維的路可能不會太順,已經不止一位發言人指出,風力發電機制造商正在尋找高模量玻璃纖維而不是碳纖維。美國能源部桑迪亞國家實驗室的轉子氣動彈性主管BrandonEnnis引用市場信息咨詢公司MAKE提供的數據進行分析,提出價格和供應鏈問題以及制造敏感性問題正是風力渦輪機制造商努力擺脫碳排放的原因。
Ennis強調,風能應用需要碳技術人員從航空航天的性能設計轉向成本驅動的設計。盡管在2015年碳在4-8兆瓦的渦輪葉片中沒有什么應用,但他說Sandia,ORNL和蒙大拿州立大學已經開始進行為期兩年的聯合研究,評估具有成本競爭力的定制碳纖維復合材料在風力渦輪機葉片中應用的商業可行性。所以他說未來在5兆瓦以下和10兆瓦以上的渦輪機中使用一些碳材料還是可能的。
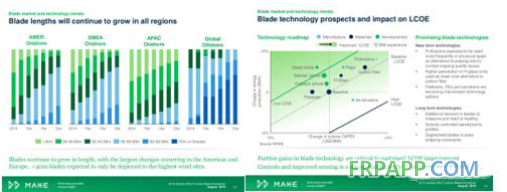
上圖是Sandia在會議演講中引用來自MAKE咨詢公司的數據
復合材料回收
2017復合材料會議召開期間,就復合材料的回收問題成立了一個小組,小組由復合材料回收技術中心的Geoffrey Wood主持,小組成員包括通用汽車公司的Mark Voss和勒克斯研究公司的Anthony Vicari等人。
Geoffrey Wood強調復合廢料流可以通過打開全新的市場,使碳纖維銷量變高,因為碳纖維增強復合材料的產品成本將會更低。所有的專家小組成員也都認為,隨著自動化程度和零件加工效率的提高,未來廢鋼產量將會減少,復合材料行業還有很多事情要做,以便搶占更替環節的領導地位。
會上,眾小組成員都認為因為使用變廣,碳纖維增強樹脂材料對有效回收利用技術的依賴性更高。雖然目前大多數回收利用都集中在碳纖維增強樹脂材料加工工藝的廢料上,但是發言人指出,回收廢舊復合材料部件的需求日益增加,到本世紀20年代后期將占回收廢棄物的很大一部分。
會上小組成員間的交流有很多亮點,現一一摘錄:
【來自ELG碳纖維有限公司的Frazier Barnes 】
【來自ELG碳纖維有限公司的Frazier Barnes 】
數據顯示,可回收碳纖維的市場可達55,000噸/年,每年可提供50,000噸回收廢料。Barnes指出,碳纖維每年預計產量12萬噸,但是需求量高達2.5萬噸/年,之間的巨大差距可由回收碳纖維來彌補。同時,回收碳纖維比回收金屬和塑料更具競爭力。
目前ELG公司在回收碳纖維上已經做出一些成就,他們的碳回收材料已經在美國的19輛車上進行了6個月的道路測試。如果此次測試通過的話,每年將有20萬輛車在車身上利用6公斤的碳回收材料。除此項目外,其他可商業化生產的項目包括:
①導軌轉向架:使用壓縮成型預浸料、80%碳回收纖維和20%原碳纖維制成的碳纖維增強樹脂材料導軌轉向架構架,可使切割重量減輕75%,輪對軌載荷減少40%。
②汽車油盤:使用包覆碳纖維填充熱塑性塑料的碳回收纖維制造墊坯,一次性實現凈形部件,與玻璃纖維增強塑料(GFRP)相比,可節省30%的重量。
③座椅:相對于13公斤的原始金屬部件,用碳回收材料可提供重量僅為2.5千克的部件。
對于目前尚未解決的難題,Barnes認為,回收碳纖維面臨的最大挑戰是鑒定和顯示纖維和部件的一致性。
【來自波音公司的Tia Benson Tolle 】
波音公司的目標是零廢物制造,包括零填埋垃圾,零危險廢物,零吸水量和溫室氣體排放量。Benson Tolle說,實現這一目標的關鍵是使復合材料部件的制造變得更加有效,最大限度地“從上到下”減少廢物。
【來自Carbon Conversions Inc.的Mark Janney 】
Carbon Conversions Inc.正在用碳回收纖維生產五種不同系列的產品。Janney舉了幾個閉環復合材料制造的例子,如美國甲骨文賽車隊與碳轉換公司合作,回收了其中一艘賽車游艇,新西蘭的Core Builders Composites公司用碳回收纖維產品生產下一代船只。Trek自行車車架被Crawford Composites公司重新應用到碳回收產品中建立方程式賽車。
Janney還提到在2016年后期,Hexcel對他們進行投資,資助碳轉化公司加強對重復利用和全生命周期收集處理方面的研發活動。
在討論階段,無論是ELG碳纖維公司還是碳轉化公司都有提到,碳回收產品的平整度和一致性很好,進行后期維修處理的客戶數量已經急劇減少。
【來自日本東麗工業株式會社的北野 】
北野說東麗公司位于南卡羅來納州斯巴達堡的新型碳纖維生產設施將于2018年開始運營,此前,東麗已經在日本在線生產碳回收纖維設施。
碳纖維科技技術進展
2017年碳纖維會議內容涵蓋的技術發展跨越了碳纖維技術的全部范圍,從碳纖維前體制造到剛剛提到的回收工作。會上出現很多技術亮點,現一一摘錄:
自適應模具系統
自適應模具系統由來自丹麥的ADAPA公司開發,他們的與會成員ChristianRaun對此進行了介紹。該系統使用數字控制,可用簡單設備將塑料、混凝土、玻璃和復合材料成型成各種簡單的雙曲線形狀。加工出產品也有多類,用單一的成型系統可加工出曲面半徑小于200毫米的曲面和面積大至6米×2米的平面板。
在生產中的使用的工藝包括樹脂灌注處理,熱塑性塑料的熱成型,泡沫芯的成型和UV固化樹脂復合材料的成型。
可一分鐘快速固化的預浸料
生產出可1分鐘快速固化預浸料的公司是索爾維公司,設計的初衷是能夠滿足自動化加工過程和一分鐘節拍過程的需求。這種SolvaLite730預浸料使用了高性能不飽和乙烯基酯,它的性能接近于典型的環氧樹脂,但是焓低,加工速度快,室溫穩定性好,無粘性。
索爾維公司的與會代表Lewis Williams介紹了實現一分鐘節拍過程的關鍵:
加熱過程中要預留預熱時間和運行時間;
要有快速的關閉工具;
整個模具表面的溫度應一致;
Williams說這類乙烯基酯類預浸料還有很大的發展空間,索爾維將在提高性能,降低成本的方向上繼續努力。
低成本碳纖維
低成本碳纖維是集眾人努力產出的成果,美國橡樹嶺國家實驗室進行研發,美國先進復合材料制造研究所負責商業化過程中所需要的數據資料。迄今為止研究發現的低成本碳纖維(LCCF)的質量與工業級別的碳纖維產品相當。
可再生丙烯腈
丙烯腈是碳纖維的關鍵前體,之前幾乎全部是從石油中提取,但最近南方研究公司已經設立試點工廠,發展非石油基的丙烯腈,他們用一種糖碳轉化的技術制備丙烯腈,南方研究公司的與會代表Amit Goyal對此進行了介紹。
預計到2019年該試點工廠年將產出0.5噸丙烯腈,南方研究公司的目標是在2021年底前能夠有一個年生產量達5000噸可再生丙烯腈的商業工廠。丙烯腈的商業化生產預計可使成本低于一美元每噸,如果這個數據實現的話,可再生丙烯腈將使制造成本降低15%到20%。