當前汽車行業新的輕量化解決方案必須滿足眾多的要求——它們不僅要為最終部件的減重、還要為最終部件的降本提供機遇。因此,它們需要使用成本合理的材料,而且這些材料要具有可回收的潛力。
雖然熱塑性復合材料符合這些要求,但加工方面的挑戰卻一直阻礙著其應用。
由韓國EELCEE公司開發的一種名為“QEE-TECH”的新型熱塑性復合材料預成型技術及相應的加工設備,據說為應對這些挑戰而提供了輕量化的解決方案。
QEE-TECH技術可以成形出熱塑性復合材料部件所需的復雜的三維預成型件,并降低了大批量生產熱塑性復合材料部件所需的成本和時間。所用的設備由EELCEE公司與位于韓國京畿道的機器人技術公司Robostar組建的合資企業QEESTAR制造。
為了展示這家合資企業正在不斷提升的這項技術的能力,EELCEE公司與一家提供車門模塊的汽車供應商實施了一個示范項目。
黏度太大而難于加工
與相應的熱固性材料相比,熱塑性聚合物相對較高的黏度是帶來加工問題的主要原因。
“熱塑性樹脂的高黏度對浸漬方法提出了嚴格的要求,而后續的成型操作則對預成型件的完整性和模具提出了嚴格的要求。”EELCEE公司CEO Queein Chang-Manson介紹說。
為解決這一問題,該公司正在成形預浸漬的纖維結構,然后將預浸漬的預成型件(預浸料)放入模具中,并對其包覆成型,從而通過在模外浸漬連續纖維、然后再將此預浸料放入模具中,來解決連續纖維在注射或模壓模具中出現的浸漬不良問題。
“通過在注塑和模壓成型的部件中封裝單向纖維和織物復合材料的嵌件,QEE-TECH技術在設計空間上為大批量生產的熱塑性復合材料帶來了明顯的進步,而且便于在一個單獨的部件中集成多種功能。”她解釋說,“這為設計師帶來了設計自由度,允許他們將昂貴的高性能連續纖維材料只鋪放到必要的地方,同時采用較低成本、較低性能的易流動性材料來確保形狀的自由度,以此來優化成本和性能。”
在一系列的應用中,EELCEE公司已證明了可以減重20%~30%(特殊情況下高達50%),并可以降低10%~20%的成本。
2013年,EELCEE公司在JEC亞洲展期間獲得了JEC創新獎,當時的獲獎產品是由成型商韓華集團采用三維 QEE-TECH技術為現代起亞汽車集團生產的一種熱塑性保險杠系統。
自動化的工藝
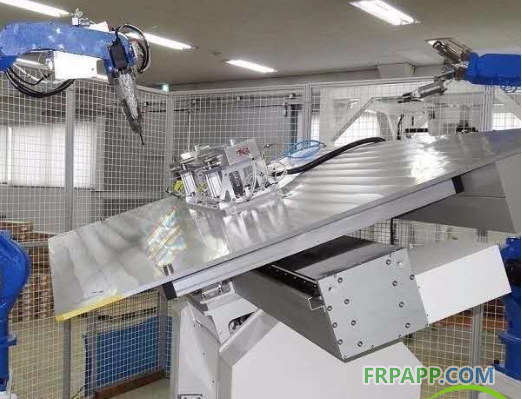
自動化的鋪層、成形、切割和浸潤。完全自動化的QEE-TECH設備采用了一種夾具,它被固定在一個可旋轉、滑動和(或)傾斜的臺面上。該裝置能快速地將材料鋪放成想要的三維形狀,由此而獲得的預成型件在得到自動切割和預浸漬后,進入注塑或模壓包覆成型操作中。這種三維預成型工藝可在60s的循環時間內完成(圖片來自EELCEE公司)
QEE-TECH三維預成型設備的設計,允許在一個單獨的操作步驟中,生產出擁有多種功能和訂制結構性能的形狀復雜的部件。
“當強度是考慮的重點時,已經證明了玻璃纖維是首選的替代材料,但如果高剛性是首要要求時,碳纖維可能是首選材料。”Chang-Manson說。
在浸潤過程中,材料通過一個預熱爐。下一步,均勻的熔融絲束沉積到一個夾具上,該夾具被固定在一個可旋轉、滑動或傾斜的工作臺機器人上。在沉積過程中,一個壓輥向絲束施加壓力。
總之,該生產裝置采用了3臺機器人——一個頭部機器人系統用于沉積材料,另外還包括臺式機器人系統和支撐機器人系統。
通過快速鋪放成一個理想的三維形狀,一個開式、訂制的三維骨架(預浸料)即被制備出來。通過一個噴氣系統,鋪放的材料得到冷卻。然后,這一成品的固體復合材料預成型件在得到自動切割后,進入包覆成型操作中。
這一完全自動化的預成型生產設備可與集成的包覆成型操作同步,從而在高達400℃的溫度下實現高效鋪層。這種三維預成型工藝可在60s的節拍時間內完成。
“QEE-TECH技術是為大批量地生產結構部件而設計的。”Chang-Manson強調說,“每一個生產裝置提供不到1min.的節拍時間,每年可生產1萬~30萬個部件。”
通常,傳統的規整或短纖維增強的聚合物(PA、PP、PET和ABS等)被用于包覆成型操作中,特別是注塑成型或模壓成型。
“這是一種非等溫的工藝。”Chang-Manson解釋說,“嵌件被預熱到剛好低于熔融的溫度,而包覆成型的材料被加熱到熔融溫度以上。由此,注塑壓力實現了低孔隙率以及嵌件與包覆成型的聚合物之間的良好粘接,循環時間與普通的注塑成型一樣。”
據介紹,在被整合成一條生產線時,這種預成型工藝沒有對包覆成型的循環時間(與注塑成型的一樣)帶來負面影響。該預成型生產裝置還可被集成到其他的復合材料生產技術中,如RTM和熱成型。
復合材料的門模塊
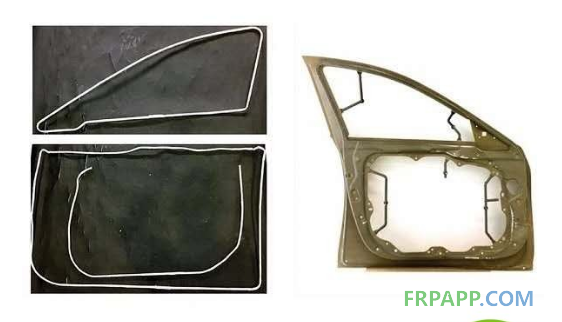
裝配連續纖維的“骨架”。QEE-TECH設備能夠對車門模塊的主要結構強度部件進行快速鋪層(左上),以創建出一些可以在模具中組合成一個開式、訂制三維骨架的片料。當被納入到一個集成的生產線中時,這種預成型工藝不影響包覆成型工藝的循環時間(圖片來自EELCEE公司)
EELCEE公司與韓國的汽車零部件制造商Duckyang實業有限公司和MS Autotech公司合作,共同開發了一種復合材料的門模塊。這項研究得到了韓國貿易、工業和能源部(MOTIE)以及韓國科學技術院(KIAT)的支持。
“這一概念的價值主要在于,為同樣價格范圍的金屬門模塊提供了減重、降本和減少子部件數量的機遇。通過采用連續纖維預成型件對熱塑性復合材料的門進行局部增強,可以實現高達20%的減重。”她補充道。
針對這一門模塊,EELCEE公司采用了一種所謂的“M-Tow”專有系統。這是一種編織系統,可將單向帶纖維絲束與一種適當的纖維編織物和(或)聚合物包封在一起,從而可以使絲束在隨后的自動鋪層過程中受熱變形,而不會對復合材料的固結帶來任何損失,也不會出現聚合物的滲出。它還允許編織的絲束能夠在任何形式的三維鋪層過程中實現自支撐。
只在所需之處使用連續纖維。這款采用QEE-TECH三維預成型件制成的熱塑性復合材料的車門僅由6個部件構成,相比之下,鋼車門有17個部件。在打開的門框架上可以看到這種包覆成型的預成型件(圖片來自EELCEE公司)
QEE-TECH工藝還允許客戶能夠針對專門的載荷引入和載荷分布而鋪成各種各樣的三維預成型件。通過適當的設計,還能夠減少子部件的數量——這種熱塑性復合材料的車門模塊僅由6個部件組成,相比之下,傳統的鋼門模塊由17個部件組成。
“在開發此部件時,需要考慮整個價值鏈的所有因素,包括:生產工藝和模具設計,裝配和使用壽命結束后。”Chang-Manson指出,“向局部引入嵌件可以提高性能,但這必然會增加復雜性。因此,非常重要的是,需要對‘在哪些方面優先考慮性能以將復雜性降到最低’作出定義。”
對車門的重新設計不僅集中在減重方面,還集中在工程強度方面。為驗證工藝的可靠性和產品的性能,EELCEE公司在采用不同材料組合和形狀配置的各種預成型件上做了廣泛的試驗。
“我們的合作伙伴對生產出的原型部件非常滿意。”Chang-Manson說,“它們尺寸穩定,而且看起來有利于大批量生產。”
據說,韓國現代汽車有限公司已在緊密跟進該車門項目,并正在考慮將此技術用于生產之中。
試驗完成后,EELCEE公司計劃聯系其他的OEMs。