日前,英國超跑Elemental RP1 的設計者采用新型制造工藝拓展了碳纖維復合材料在該款道路車上的應用。“定制鋪絲(Tailored Fibre Placement,TFP)”新工藝帶來了成本、強度和韌性的綜合解決方案, 使得碳纖維不再受限于成本和脆性的束縛。
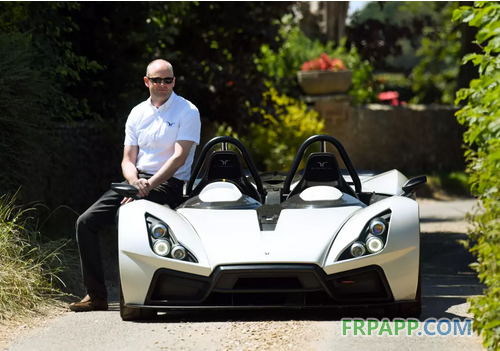
TFP生產工藝由德國TFP設備制造商ZSK公司開發,為碳纖維復合材料開拓了新的應用領域。
Elemental公司復合材料經理表示,TFP工藝改變了其對碳纖維復合材料成本與減重能力的看法,能夠使預制件快速成型,極具成本效益且更為耐用。所生產的Elemental RP1跑車的后車身結構件非常堅韌,能夠承受石塊飛濺等多種沖擊,且能夠成型具有復合曲線的復雜三維結構。而這些是傳統碳纖維復合材料部件無法實現的。
TFP工藝以縫編技術為基礎,將碳纖維合股紗或粗紗鋪設于基板之上形成二維凈成型預制件。相比于采用手工鋪放碳纖維氈進行生產的勞動密集型傳統工藝方法,該工藝減少了邊角料、提高了可操作性并降低了工藝復雜程度。TFP工藝在生產預成型件的過程中,通過巧妙地鋪絲和針刺,在模具中成型了三維結構復雜部件。
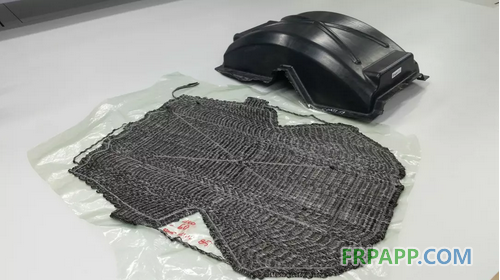
RP1 車身部件及其TFP預制件
Shape集團專長于碳纖維復合材料工具的生產,該公司已為TFP部件的設計和制造設立了專門的部門。該部門運營經理Peter McCool表示“傳統工藝受限頗多,不僅僅是設計和成本,在材料的性能方面也表現較脆,甚至不能承受敲擊或摩擦的考驗。而TFP工藝是一種靈活性高、具有成本效益的規模化生產技術,這為復合材料的應用創造了更多的機會。”
生產效率高于傳統工藝
碳纖維復合材料的傳統生產方法通常包括復雜的切割和手工鋪絲工藝,碳纖維在使用之前就已經損失了超過三分之一的用量。眾所周知,碳纖維在其纖維軸向強度最大,因此,要生產出高強部件,取向精度至關重要。
“手工鋪放是一種勞動力和能源密集型技術,出錯率高,當更多地考慮部件強度時,結果往往難以達到最佳。”McCool說,“這就導致了過度設計產生的多余鋪層。而TFP工藝允許通過精確鋪絲來實現最佳強度,從而承受外力載荷并加快開發和生產速度。”目前,采用Shape設備能夠設計碳纖維復合材料的車身部件,并采用TFP工藝生產。這些結構件能夠承載車身、后行李箱的重量,以及相當的氣動力。
TFP復合材料采用熱塑性樹脂,能夠幫助改善碳纖維的脆性。同時,在生命周期末端可以加熱至300°C回收利用,無需填埋。
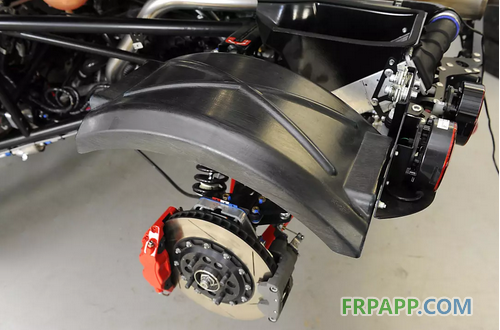
采用TFP工藝生產的復合材料后車身部件能夠承載包括氣動力在內的多種載荷