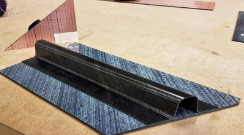
該解決方案由Institut de Soudure Group 與阿科瑪共同開發,他們為此提供了各自在焊接技術和高性能聚合物方面的專業知識。
熱塑性復合材料在航空領域的應用是未來幾年的一大挑戰,需要使用能展示良好力學性能與成本效益的焊接技術。
這項創新在于設計并建立一種擁有極高性能的工藝,允許焊接任何纖維增強的熱塑性基體材料。
該創新的焊接解決方案可實現的焊接接頭系數(與原材料相比)約為85%,操作完成后焊縫上無任何異物。
該解決方案是基于對一個接收器的使用。該接收器與焊頭中的感應線圈以及未增強的或低纖維含量的純熱塑性基體的界面層相連并隨其移動,可根據應用而訂制。焊頭在基材壓力下產生冷卻,以確保焊縫被壓實。
航空與復合材料主管Jérôme Raynal解釋說:“我們用激光高溫計測量溫度,它實際上是從側面測量接收器的邊緣, 這樣我們就能知道界面的溫度。我們還有一個在焊接表面加壓吹氣的冷卻裝置來確保溫度低于結晶溫度,因此,一旦釋放壓力,就不會有壓實松動的風險。”
這種帶有移動接收器的創新焊頭非常緊湊,允許得到精確而復雜的應用。該創新的焊接解決方案采用的焊頭被安裝在一臺六軸機械手臂上,操作完全自動化。其主要優勢是:
? 高性能焊接(最小焊接接頭系數為85%);
? 減少了后處理(無需粘合劑或膠帶以及化學品);
? 減輕了重量;
? 在焊接接頭處無支撐物;
? 動態和全自動化/監控解決方案;
? 生態影響:使用可回收材料,且由于局部加熱,因而能耗低;
? 適用于任何熱塑性基體材料和任何纖維。
Institut de Soudure Group開發復合材料焊接技術已有10多年,如電阻焊、共固焊和感應焊等幾種技術。
針對與Stelia Aerospace 合作開發的ARCHES BOX TP示范項目(已在2017巴黎航空展上亮相),該集團負責采用動態感應焊接工藝,對蒙皮上的縱梁進行焊接。該項目是航空結構件感應焊接技術發展的開端。
基于這一發展,Institut de Soudure Group與熱塑性材料供應商阿科瑪開發了這項新技術,目的是改善傳統感應焊的弱點:從2019年起,與Stelia Aerospace 和Latecoere等主要航空公司合作的一些研究項目已經啟動,以評估所開發的解決方案;從2020起,主要目標是提高技術成熟度,參與特定的航空項目,以獲得資格認證。