在航空航天和電動汽車等領域的應用中,碳纖維因輕質高強的特性而備受歡迎。以往,人們在提高CFRP的強度時,通常只考慮優化纖維的取向。
近日,東京理科大學的研究團隊采用新的設計方法,能夠同時優化纖維的厚度和取向,進一步減輕復合材料的重量,有助于開發更輕的飛機和汽車。
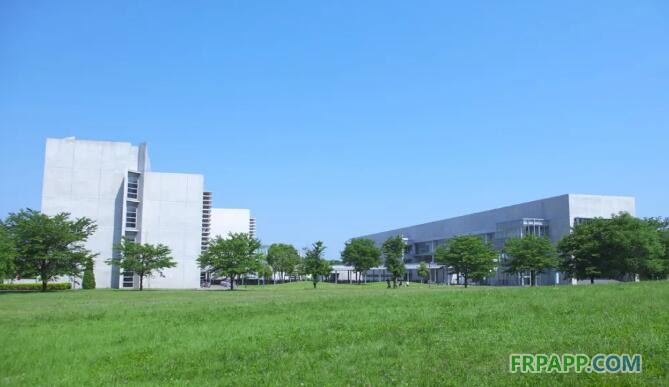
CFRP因其抗拉強度、剛度和比強度而聞名。為了提高其強度,研究方向主要集中在一種名為“纖維取向設計”的技術上,通過優化纖維的取向來提高其強度。
東京理科大學的Ryosuke Matsuzaki博士表示:“此法只能優化纖維取向,無法改變纖維厚度,不利于充分發揮CFRP的機械性能。”
有鑒于此,Matsuzaki博士及其同事提出新的設計方法,可根據復合結構中的受力位置,同時優化纖維方向和厚度。與恒定厚度線性層壓模型相比,可在不影響強度的情況下減輕CFRP的重量。
該方法共分三步,包括預備、迭代和調整過程。
在預備階段,通過有限元法(FEM)進行初始分析,確定層數,通過線性層壓模型和具有厚度變化模型的纖維取向設計進行定性重量評估;在迭代過程(iterative)中,根據主應力方向確定纖維取向,并根據“最大應力理論”迭代計算厚度;最后,在調整過程中,首先在需要提升強度的區域創建參考“基礎纖維束”,接著將各纖維束排列分布在參考束的兩側,確定最終的方向和厚度。
比起纖維導向方法,通過這種同步優化法,可以使材料減重超過5%,同時實現更高的載荷傳遞效率。研究人員希望通過這種方法進一步減輕傳統 CFRP部件的重量,以“制造出更輕的飛機和汽車,幫助實現節能減排的目標。”