一、纏繞制品的結構
纏繞工藝制造的管、罐等產品結構大體分為3層:內襯層、結構層和外保護層。
(1)內襯層。內襯層是制品直接與介質接觸的那層,它主要作用是防腐、防滲、耐溫。因此,要求內襯材料具有優良的氣密性、耐腐蝕性,并且耐一定溫度等。
內襯材料有金屬、橡膠、塑料、玻璃鋼等不同材質。根據不同用途與生產工藝要求來選定,作為化工防腐用時,則玻璃鋼內襯是最佳選擇。這樣即可避免粗而重的金屬制品,又可避免內襯層與結構層之間粘接的麻煩。并且,這種玻璃鋼內襯適應性強。通過改變內襯材料的種類、配方,使之在可以滿足化工防腐上各種不同工藝的要求。根據容器內所貯存介質的種類、濃度和溫度等技術要求選擇內襯材料。
(2)結構層。結構層又稱為增強層。它的作用主要是保證產品在受力的情況下,具有足夠的強度、剛度和穩定性。而增強材料——玻璃纖維則是主要的承載體,樹脂只是對纖維起粘接作用,并在纖維之間起著分布和傳遞載荷的作用。因此選擇高強度、高彈性的增強材料和性能良好的樹脂是提高結構層承載能力的重要因素。這對航空及軍用產品尤為重要。對于普通工業防腐及民用產品,在保證產品具有足夠的承載能力的前提下,還要從經濟成本、工藝性能等因素綜合考慮,選擇增強纖維和樹脂。
另外,結構層的承載能力還要受到纖維纏繞方向的影響,要求增強層在不同方向上具有不同的強度。這時,可以通過結構計算確定纏繞角。例如,對內壓容器,確定合適纏繞角,使環向強度與軸向強度相比,近似等于內壓載荷所引起的環向應力和軸向應力之比。目前,采用最多的纖維鋪設方式有螺旋纏繞和環向纏繞兩種,有時可將這兩種鋪設方式進行組合,使螺旋方向纏繞承受軸向應力,環向纏繞則主要承受環向應力。試驗研究表明,對于內壓圓筒型容器,組合纏繞型比單一螺旋纏繞更有效;而對于外壓圓筒型容器,加筋是加強層提高承載能力的一種結構形式,例如:地下管道、貯罐采用加筋形式會更有效地抵抗由土壤所產生的壓力(外壓力)所引起的變形和翹曲。
隨著復合材料技術的不斷發展,采用夾層結構(如:夾砂層)纖維纏繞可有效提高玻璃鋼管的剛度,夾層結構管材的強度高、剛度大、重量輕、造價低、使用壽命長、耐腐蝕、無毒無味等特性,優于傳統的鋼管、預應力水泥管、鑄造管等。隨著夾層結構管技術的發展,夾砂(石英砂)纖維纏繞玻璃鋼管材正逐步取代傳統的輸水管材。如河北中意玻璃鋼有限公司生產的玻璃鋼貯罐、工藝管和夾砂纖維纏繞管等產品。
(3)外保護層。一般情況下為了延長玻璃鋼制品的使用壽命,不僅要求內襯防腐性能好,加強層具有足夠的承載能力,而且要求產品外表面也應具有一定的防護性能,特別是對于露天的設備。對于安裝在室外的玻璃鋼制品,間苯二酸型或雙酚A型樹脂中加入石蠟,就足以保護制品8~10年。由于紫外線光可損害聚酯樹脂,因此當采用聚酯樹脂時宜添加紫外光吸收劑,可以將紫外光轉變成熱能或次級輻射出去,大大降低產品變黃的速度,提高透光率,從而提高玻璃鋼的耐候性。一般情況下要嚴格限制這類材料的使用,必須使用時,要盡可能地使其價格和對聚酯樹脂改變的性能減至最小。紫外線吸收劑的使用量(按樹脂質量計)為:0.2%~0.5%。
二、纏繞制品的應用
由于纏繞玻璃鋼制品具有上述各特點,因此,在化工、食品釀造業、運輸業及軍工等方面獲得比較廣泛的應用。
1. 管道
纖維纏繞管道制品因其強度高、整體性好、綜合性能優異、容易實現高效的工業化生產,綜合運營成本較低而被廣泛地應用于煉油廠管道、石油化工防腐管道、輸水管道、天然氣管道和固體顆粒(如粉煤灰和礦物)輸送管道等方面,如圖下圖所示。
目前,美國各地用的纖維纏繞管道總長占整個運輸工具的三分之一,所負擔供應的能量(包括石油、天然氣、煤、電)占全國需用量的一半以上。在我國工業生產中,纖維纏繞管道同樣已被大量地采用。圖7-35為新疆某輸水重點工程成功采用的Ø3.1m玻璃鋼管,單管長12m,重16噸,工程一次安裝通水成功無泄漏。
2006年北京高碑店電廠煙塔合一除硫系統中,煙氣管道采用ECR纖維增強乙烯基酯樹脂制作的玻璃鋼管,直徑達7m(如下圖所示),以立式纏繞機與臥式纏繞機現場制造,質量甚得好評。
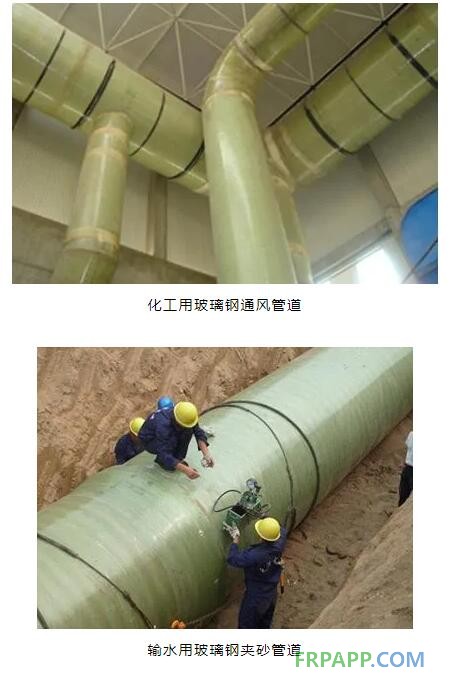
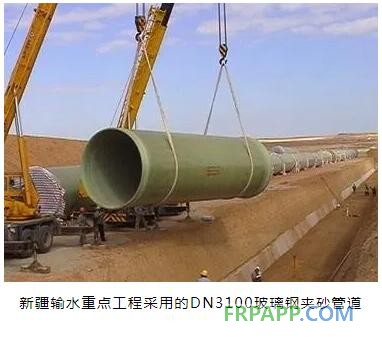
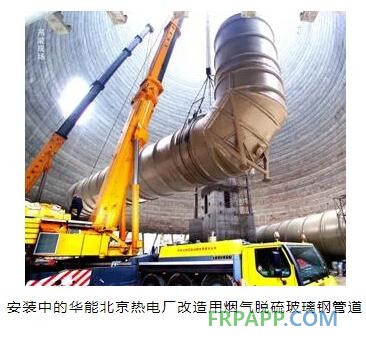
纖維纏繞管道在我國市場需求量巨大、前景廣闊,尤其表現在油田應用方面,如:
(1)大慶油田每年新增油水井2500多口(2005年5000口),管道總需求2000km,其中高壓注水管道為500 km,油田改造項目計劃需油田管線為1000 km左右,以每公里管線工程費用15萬元計算,大慶油田每年用于管道的工程費用可達3億元以上;
(2)吉林油田每年管道需求在1000km左右。其中高壓玻璃鋼管道在500km以上;
(3)遼河油田每年管道總需求為1800 km左右,其中高壓注水管為600 km以上;
(4)勝利油田每年管道總需求2200 km,其中高壓注水管為1000 km以上;
(5)大港、華北、中原、江漢、江蘇、新疆、青海、長慶等其他油田的高壓玻璃鋼管材的需求量也逐年增加,全國每年油田系統的玻璃鋼管材的總需求量可達6000 km以上,工程投資可達9億元以上,其中70%以上的管線可由高壓玻璃鋼管道替代。
另外具有強勁市場態勢的井下油管,其市場需求量比高壓玻璃鋼地面管線管更大。
2. 儲罐
儲運化工腐蝕液體,如堿類、鹽類、酸類等,采用鋼罐很容易腐爛滲漏,使用期限很短。改用不銹鋼成本較高,效果也不及復合材料。采用纖維纏繞地下石油儲罐,可防止石油泄漏,保護水源。用纖維纏繞工藝制成的雙層壁復合材料儲罐和管道,已在加油站獲得廣泛應用。
這類儲罐和管道通常用E玻璃纖維/不飽和聚酯樹脂制成,在制造過程中可通過加入石英砂或其它填料來提高剛度,降低制造成本。圖即為化工用的大直徑玻璃鋼儲罐。
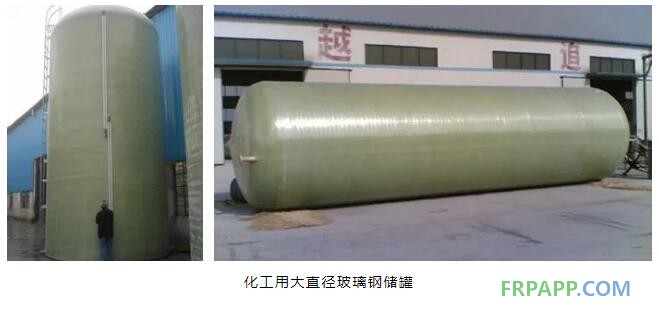
3. 壓力制品
纖維纏繞工藝可用于制造承受壓力(內壓、外壓或兩者兼俱)的壓力容器(包括球形容器)和壓力管道制品(如圖7-38所示)。纏繞壓力容器多用于軍工方面,如固體火箭發動機殼體、液體火箭發動機殼體、壓力容器、深水外壓殼體等。纏繞壓力管道可充裝液體和氣體在一定壓力作用下不滲漏、不破壞,如海水淡化反滲透管和火箭發射管等。先進復合材料的優異特性使纖維纏繞工藝制備的多種規格火箭發動機殼體和燃料儲箱得到成功的應用,成為現在乃至將來發動機發展的主方向,它們包括小到直徑只有幾厘米的調姿發動機殼體,大到直徑3米的大型運輸火箭的發動機殼體,如下圖所示。
纖維纏繞復合材料壓力容器已在航空、航天、造船等領域獲得廣泛應用。用碳纖維和芳綸纖維纏繞的薄壁金屬內襯高壓容器以其高結構效率、高性價比優勢成為航天飛機和人造地球衛星的首選。所用的內襯材料包括不銹鋼、鈦合金、鋁合金和熱塑性塑料等。容器充裝的介質有氮氣、氧氣、氫氣和氦氣,形狀多為環形、球形(如圖所示)和扁橢球形,直徑范圍從0.3~1.01米。
小型壓力容器已在個人生命保障系統獲得成功應用。屬于這類用途的容器有消防員供氧器(如圖7-41所示)、登山隊員的供氧器等。這類容器大多用芳綸纖維/環氧樹脂或玻璃纖維/環氧樹脂制成,具有重量輕、便于攜帶、高疲勞壽命和高可靠性的綜合特性。纖維纏繞工藝制造的壓縮天然氣(CNG)氣瓶如圖所示,已經成為標志性的新型能源載體。
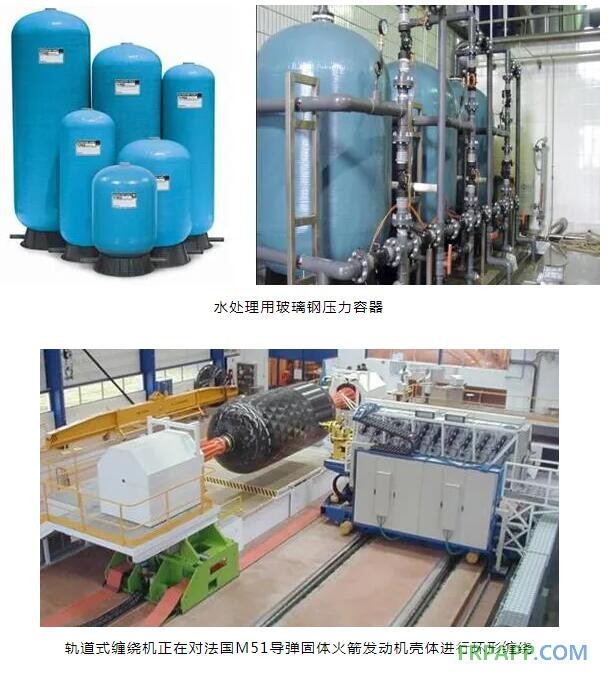
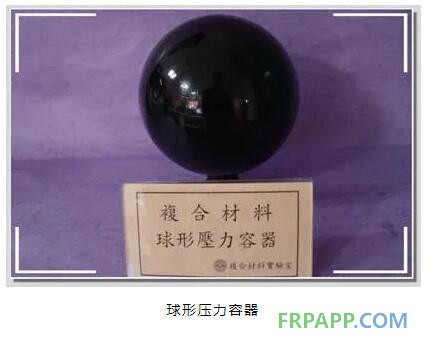
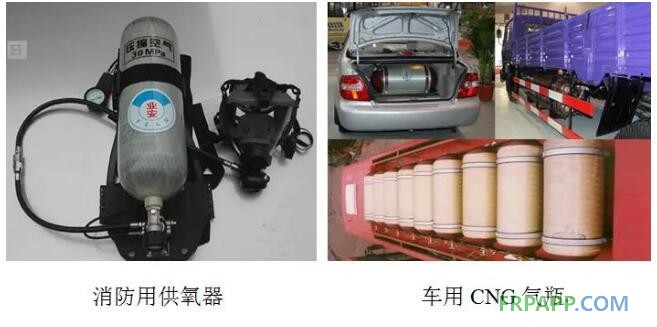
1986年至今,我國已生產玻璃鋼/復合材料呼吸氣瓶、CNG(壓縮天然氣)瓶和燃料電池用氫氣瓶等超過15萬只。1997年我自主研發的環形壓力容器投入使用。2006年我引進德國技術裝備(內襯制造、纖維纏繞),在蘇州建立年產能達11萬只復合材料氣瓶的生產基地。中材科技(蘇州)公司生產的復合材料氣瓶已成為全球四大品牌之一。
4.其他
在機械工程上有時需要輕質高強的部件如新型無梭紡織機上的劍桿,是代替“梭子”穿線的,來回往復速度快,要求輕質、高強、剛度大,在此方面纖維纏繞工藝制備的碳纖維/環氧復合材料管具有其它材料無法比擬的優勢。
復合材料轉動軸如圖所示,是為宇航工業提出并得到應用的,主要用于直升飛機,如尾旋翼長套軸、主旋翼厚壁轉動軸等。1986年冷卻塔工業開始采用復合材料轉動軸,這種傳動軸的主要優點為耐腐蝕、重量輕、振動小、壽命長。
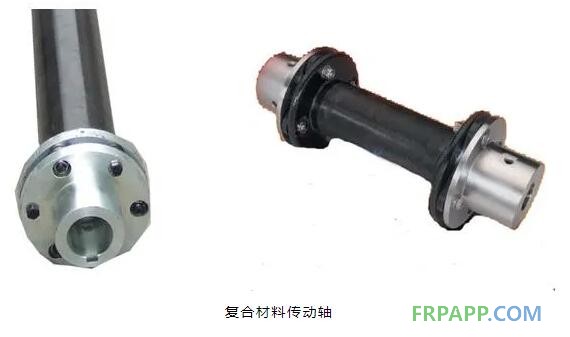
電氣設備中的開關裝置、高壓熔斷器管、回路斷路器及高壓絕緣體等均可采用纖維纏繞工藝制造,在這些制品中纖維纏繞復合材料爆破強度高,電絕緣性能好的特點得到充分的發揮。此外大型電機上的綁環和護環、車用飛輪轉子等也是纖維纏繞復合材料制造的,其比強度高、線膨脹系數小、蠕變率低,絕緣性能良好,非磁性和性價比遠優于無磁鋼。
纖維纏繞復合材料在電氣工程上應用很廣,可用纖維纏繞技術制造輸配電電線桿、天線桿及工程車臂桿等。
纖維纏繞制品在體育器材方面的應用,會使競技體育提高到一個新的水平,所以發達國家在這方面均有大量人力與資金的投入。如纖維纏繞高爾夫球拍桿、滑雪杖、羽毛球桿、獵槍管均可采用碳纖維/環氧復合材料制造,如圖所示。
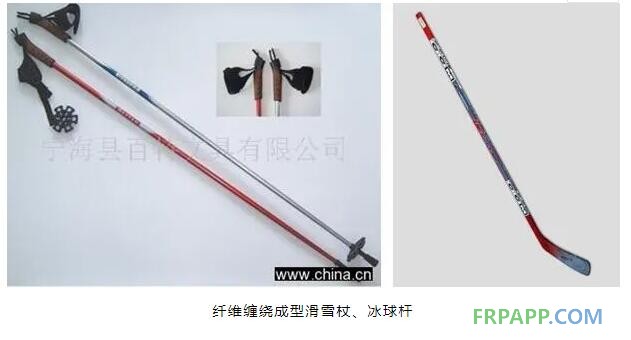
三、典型纏繞制品
1. 大直徑儲罐
自20世紀80年代以來,具有輕質高強和耐腐蝕等特點的玻璃鋼儲罐在我國石油、化工、冶金、釀造、環保和醫藥等領域獲得越來越多的應用。最初由于成型工藝和交通運輸等方面的原因,玻璃鋼儲罐直徑一般小于4m。近些年來,隨著我國經濟的持續增長,市場上對大直徑儲罐的需求量迅速增加:
(1)油田方面
國內幾個大油田如大慶油田、勝利油田和江漢油田等均使用了大直徑玻璃鋼儲罐。以大慶油田為例,該油田僅在1995年一年內至少使用了2臺直徑10m、2臺直徑7.5m和7臺直徑5.5m的大直徑玻璃鋼儲罐。目前該油田大直徑玻璃鋼儲罐的使用量已有幾十臺,最大直徑達10m。2006年11月,在中原油田采油二廠濮三污水站水質治理改造工程中建成300m3緩沖罐2座,1000 m3 收油罐2座,采用以機械纏繞為主、手工糊制為輔的制造工藝,主體設備在現場制作。
(2)化工領域
化工領域是大直徑玻璃鋼儲罐的另一個重要的應用領域。國內一些大的化工企業,如云天化工集團、錦州化工集團和蘇州化工集團等單位均在其技改中選用了大直徑玻璃鋼儲罐。其中,蘇州精細化工廠使用的直徑11m的玻璃鋼儲罐據稱為國內在用的最大直徑的纏繞成型玻璃鋼儲罐。
(3)冶金行業
冶金行業是大直徑玻璃鋼儲罐的又一個重要應用領域,如1995年銅陵有色公司選用的填料塔、空塔沉降槽及填料塔沉降槽,1996年銅陵金屬工程公司選用的一級動力波、氣體洗滌塔和二級動力波等設備均為大直徑玻璃鋼儲罐制作而成。
目前纏繞玻璃鋼儲罐可達的最大直徑為25m,以儲存2.5萬噸原油計算,儲罐的高度達63.7m,因此多采用立式、現場纏繞成型。
在立式纏繞中,模具放置在托架上保持模具表面與地平面垂直,通過幾個可伸縮的懸臂將托架固定在模具中央一個大的軸承上,此軸承由液壓驅動,通過管線與模具旁不遠處的一個液壓泵相連。纏繞小車軌道垂直立于模具旁,整個裝置由微機控制,纏繞時,模具水平旋轉,小車在軌道上上下運動,利用二者之間的相對運動完成纏繞。通過計算機控制程序輸入不同的纏繞角,即可控制模具旋轉與小車運動之間的相對速度,從而分別實現螺旋或環向纏繞。立式纏繞的最大特點是:由于可伸縮懸臂的長度具有可調性,所以,和其他方法相比,它可生產出更大直徑范圍的玻璃鋼儲罐。利用此法纏繞出直徑為25m的玻璃鋼儲罐,為世界上最大直徑的纏繞成型玻璃鋼儲罐。
為克服產品的運輸問題,大直徑儲罐多采用現場纏繞(如圖所示),即將玻璃鋼儲罐的生產設備拆成若干部分,連同原材料一起運至現場,再將設備拼裝起來,進行生產。此法優點是可克服交通條件給大直徑玻璃鋼儲罐運輸帶來的制約。
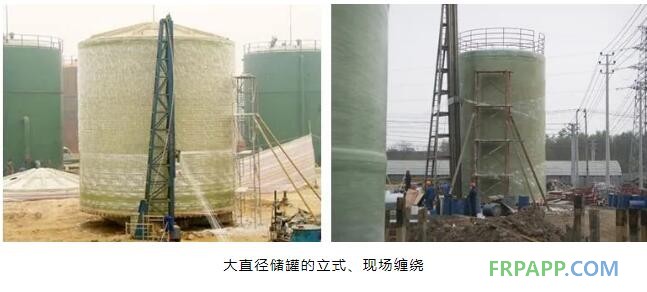
在結構設計方面,立式儲罐罐體的不同高度受靜壓不同,因此不同高度的罐壁可具有不同的厚度。為節省材料、降低成本,罐體壁厚多采用上薄下厚的結構形式,并綜合各種不同的影響因素,其中重點考慮風壓及震載的影響,編制計算機程序進行運算。
在鋪層設計方面,玻璃鋼儲罐罐壁一般由以下3層組成:
(1)內層
內層由富樹脂層及中間層組成。富樹脂層由內襯樹脂加有機纖維聚酯氈增強,樹脂含量90 %以上,厚度控制在0.5mm左右,主要提供制品的耐腐蝕性和防滲透能力。中間層由內襯樹脂和無堿玻璃纖維噴射紗組成,樹脂含量控制在70 %~80 %,厚度控制在2mm左右,主要是保護富樹脂層,提高內層的抗內壓失效能力,阻止裂紋擴散。
(2)結構層
結構層即增強層,采用無捻玻璃纖維粗紗和玻璃織物(或短切纖維氈) 增強,承受拉應力、壓應力和各種外載荷,保護內層。結構層的最內層設計為環向層,因為其不僅容易鋪墊在最里層,而且容易通過調整往復行程的距離來滿足各分段不同壁厚的要求;結構層的中間層設計為大角度縱向層,以抵抗運輸、安裝、風載和地震等諸多復雜工況下產生的縱向應力;結構層的最外層設計為環向層,以使整個結構層形成“反對稱”的結構形式,避免拉彎耦合效應。結構層的厚度按靜液壓、風載和震載等載荷條件計算確定,樹脂含量控制在30 %~40 %。
(3)外層
外層即外富樹脂層,樹脂含量大于90 %,厚度控制在1.5mm左右。采用玻璃纖維表面氈增強,也可采用0.1~0.2mm薄玻璃帶增強,同時在樹脂中加入紫外線吸收劑以防止老化。該層主要是保護外壁不受外界機械損傷和防紫外線老化。
在選擇原材料時,玻璃鋼儲罐堅持質量優先、兼顧價格的原則,由于各層的作用不同,在材料選用上各有不同:內襯層直接與介質接觸,其材料選擇對控制纏儲罐的滲漏起關鍵作用,儲存酸性介質通常選用乙烯基樹脂,儲存堿性介質采用雙酚A型樹脂,如197#樹脂,要求儲罐耐水則采用如189#樹脂,要求儲罐耐堿、耐水采用無堿玻纖,耐酸用中堿玻纖,內襯則采用表面氈、短切氈共同增強,以便提高含膠量,增強抗滲能力;結構層主要滿足儲罐的強度及剛度要求,選材應充分考慮所選樹脂基體必須與纏繞用玻纖有良好的浸潤性,以便形成致密的結構;外表面與外界環境直接接觸,按耐老化要求選材。
在成型工藝方面,儲罐壁成型時制造圓柱形帶封頭的模具,分以下四步進行:
(1)手糊成型內層中的富樹脂層;
(2)噴射成型內層中的中間層;
(3)立式纏繞成型結構層;
(4)手糊成型外層。
儲罐制造完畢后,須對罐體進行氣檢,檢查其強度、剛度及密封性。若儲罐存在氣眼、氣孔等缺陷,充氣氣壓將無法保證,則須查找缺陷處,然后及時采取措施處理。
2. 反滲透膜殼
反滲透是用足夠的壓力使溶液中的溶劑(一般常指水)通過反滲透膜(一種半透膜)而分離出來,方向與滲透方向相反,可使用大于滲透壓的反滲透法進行分離、提純和濃縮溶液。利用反滲透技術可以有效的去除水中的溶解鹽、膠體,細菌、病毒、細菌內毒素和大部分有機物等雜質。反滲透膜的主要分離對象是溶液中的離子范圍,無需化學品及可有效脫除水中鹽份,系統除鹽率一般為98%以上。所以反滲透是最先進的也是最節能、環保的一種脫鹽方式,也已成為了主流的預脫鹽工藝。反滲透技術的應用范圍包括:
?制藥、醫藥行業無菌、無熱源純化水制取;
?電子、電力行業用超純水;
?生物醫藥用水;
?化工、化妝品配料用水;
?苦咸水、海水淡化;
?電鍍涂裝行業所用溶液配給,零件清漂洗;
?精密機械、特種材料,光電材料,石英制品行業用的清洗,配給,冷卻水;
?飲用純凈水、食品飲料用水。
反滲透膜殼是反滲透設備的重要組成部分,用以承受膜法分離提純時施加的壓力,最初多為不銹鋼材質,隨著纖維纏繞工藝水平的提高,玻璃鋼膜殼的應用越來越廣,其特性優點包括:
(1)基于復合材料結構的可設計性,可以通過改變玻璃纖維的含量和分布,在一定范圍內獲得不同強度和彈性性能的玻璃鋼膜殼,以承受不同的載荷。如對于雙向受力的結構,可以考慮雙向鋪層或多向鋪層的方式,選用適當的纖維用量或改變各單層的鋪層方向,以滿足結構性能要求,實現容器在工作壓力條件下處于最佳的受力狀態,充分發揮制品的結構性能,真正體現出“輕質高強”這一概念。
(2)纖維纏繞具有良好的工藝性,可根據產品的尺寸、形狀和結構特性等進行綜合設計,以最大限度地減少成型、加工次數或只需一次成型即可,縮短生產周期,減少能源消耗。
(3)在室溫條件下,玻璃鋼的導熱系數一般在0.15-0.36w(m.k)范圍內,大約僅是金屬材料的1/100-1/1000,其絕熱性能是金屬材料所無法比擬的,這一特性使得玻璃鋼膜殼能對反滲透膜起到良好的溫度變化保護作用。
(4)玻璃鋼膜殼具有突出的耐腐蝕性,通過合理的選材和適當的工藝,玻璃鋼不僅對多種低濃度的酸、堿、鹽介質及溶劑有良好的穩定性,而且有良好的抗大氣、海水和微生物的性能。
目前國內已有多家玻璃鋼反滲透膜殼的生產廠家,哈爾濱樂普等國產膜殼的質量和技術已達到國際先進水平、進軍國際市場,如圖所示。
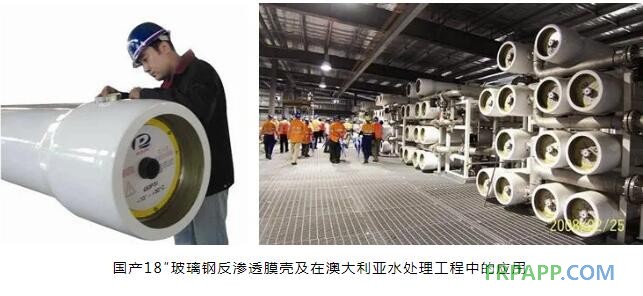
3. CNG氣瓶
隨著世界經濟的發展,全世界的汽車產量和汽車保有量都在不斷增加,依據國外1994年的研究報告及世界上石油的蘊藏資源和消耗量的預測,到21世紀中葉,汽車以石油作燃料的時代將會結束。天然氣作為汽車燃料是一種燃燒干凈、價格便宜而又使用安全的氣體,因而發展燃氣汽車成為未來重要的發展方向。燃氣汽車的重要和關鍵零部件之一是CNG氣瓶,這類氣瓶綜合了復合材料的高比強度、可設計性以及內襯的良好氣密性、優良的耐蝕性等諸多優點,使其達到高承壓能力、高疲勞壽命、質輕、耐腐等優良性能的完美結合,這也使得對復合材料CNG氣瓶的研制開發成為國內外的一大熱點。
在同樣容積和壓力下,復合材料CNG氣瓶比鋼質氣瓶的重量可減輕1/3~2/3,二者相比較,顯然復合材料CNG氣瓶在汽車運行節能上更具有優勢;同時復合材料在受到撞擊或高速沖擊發生破壞時,不會產生具有危險性的碎片,從而降低或避免了對人員和車輛的損害。
近年來,隨著復合材料成本的降低,成型工藝的不斷改進,使得復合材料CNG氣瓶在國內外倍受青睞,尤其在轎車和輕型車上的應用極具競爭力。復合材料CNG氣瓶是先通過拉伸、旋壓等工藝制成鋁膽,并在鋁膽外采用高強度纖維纏繞。國外已經用它來取代鋼制氣瓶。1994年我開始開發CNG氣瓶,并首先在首都公交車上裝車使用(一輛車用90升氣瓶9只),目前北京已成為世界城市中以CNG為動力的公共汽車擁有量最多的城市。
由于復合材料氣瓶采用不同的材料制成,在荷載作用下,表現出的應力狀態不同:鋁膽為彈塑性材料,而外部的纖維一般采用高強度纖維及碳纖維、環氧樹脂、有機纖維、環氣樹脂等纏繞而成,具有比強度大,比剛度高等諸多優點,如碳纖維T300/環氧5208的比強度是鋁的6.3倍,比剛度是鋁的4.16倍。對于這種基底為塑性、表面采用脆性的纖維來增強的復合材料,基體的破壞應變通常比纖維的破壞應變高得多,往往在基體進入塑性狀態時,外部纖維材料仍處于彈性狀態。從失效方式上看,復合材料瓶體的失效往往是鋁膽先出現龜裂,鋁膽的開裂使氣瓶漏氣是復合氣瓶早期破壞的主要原因之一。另外,纖維與基體復合后,會改變它們原有的強度性能,如纖維與基體粘牢后的,即使某一纖維斷裂,也只影響局部應力分布。圖7-47即為CNG氣瓶在汽車上的應用。
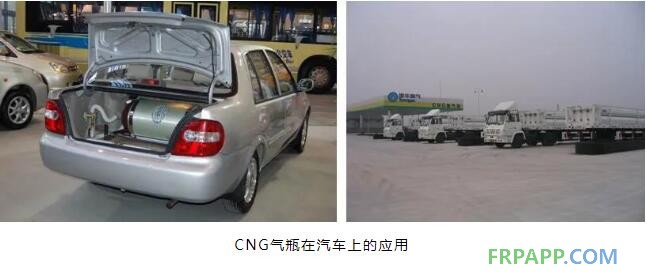
4. 夾砂管道
縱觀我國玻璃鋼夾砂管及設備的發展歷程,在16年來的不斷探索、研制和開發過程中,得到了飛快的發展。
(1)第一代加砂工藝:從國外引進的上加砂,兜砂紙兜砂
從1993年開始,以引進意大利加砂工藝和設備為主,這種工藝和設備是由模具上方通過皮帶輸送機將石英砂灑落到模具上方,用兜砂紙將石英砂兜住,靠淋膠頭向石英砂外層淋樹脂,不加滾壓,如圖所示。
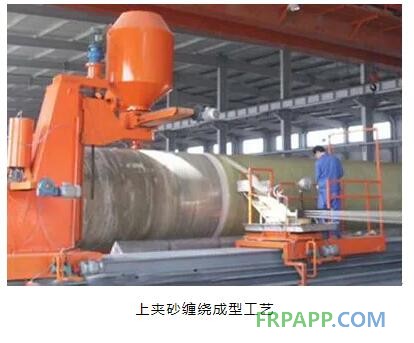
這種工藝和設備的缺點主要有三點:1、由于兜砂紙強度低,張力小,石英砂層無法施加滾壓,因而石英砂層密實度低、氣孔多、剛度差、樹脂含量高,造成質量不穩定,成本高;2、由于兜砂紙強度低,對樹脂浸透能力差加之設備輸膠能力不夠,造成每次加砂層的厚度不能超過3一5mm,生產效率低;3、石英砂是以自由落體形式灑落到模具上方,灑落過程中產生大量粉塵,如模具稍有偏心或轉速不均,落到模具上的石英砂厚度就厚薄不均,夾砂管外表面不可能平整。
(2)第二代加砂工藝:國內企業改進的上加砂,兜砂布兜砂
起于90年代末,為克服第一代加砂設備和工藝的缺點,在設備構造和材料上作了大量嘗試和改進:1、采用大流量輸膠系統,并經改進后將樹脂噴淋到石英砂里層,樹脂通過擠壓從里向外滲透,減少了樹脂用量和損耗,降低了成本;2、增加了機械液壓裝置,提高了石英砂的密實度和管道的剛度及表面平整度;3、采用高強度兜砂布,使一次夾砂層厚度提高到6-8mm,提高了生產效率。缺點是:加砂工作面高、操作不方便、粉塵較大,仍存在加砂層厚度不均現象,生產效率不高。
(3)第三代加砂工藝:下加砂和分層淋料下加砂(圖),兜砂布兜砂
2000年下半年研制,這種工藝是在纏繞工作臺的對面通過一套下加砂裝置將石英砂預浸上樹脂,以靜態方式,始終跟模具同步的轉速把石英砂用兜砂布從模具下方緊緊裹到管芯模上,樹脂通過從上到下水平振動、從里向外擠壓滲透,滲透中利用了離心力作用,加快了樹脂滲透速度,提高了樹脂分散均勻性,生產過程機械化,不拋灑,粉塵小,樹脂含量低,厚度均勻、平整度好。但為達到管道的質量穩定,需把夾砂層內的樹脂含量控制在20%以上才能使管道的力學指標穩定,管道成本降不下來。
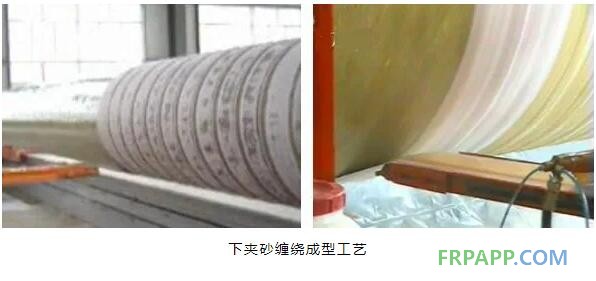
(4)第四代加砂工藝:濕法攪拌下加砂
2004年由衡水華成玻璃鋼有限公司研制成功,有自主知識產權。這種工藝是用加砂裝置將石英砂和樹脂攪拌均勻,通過輸砂平臺,用兜砂布把石英砂從模具下方緊緊裹到管芯模上,通過機械碾壓裝置對夾砂層進行同步碾壓。這種工藝的優勢有以下幾方面:
①加砂前預先攪拌砂漿,可以精確控制夾砂層的樹脂含量,控制成本;
②生產效率高,加砂與碾壓、環向纖維纏繞可同步進行;
③加砂層氣孔非常少,夾砂層的密實度和平整性很好,力學性能高(彈性模量高);
④加砂厚度可控制,一次加砂厚度為5-30mm,可精確控制;
⑤在保證管道質量的前提下,大大降低了管道原材料成本。